Why Rely on a Flanged Connection?
- Robert Robinson
- Feb 18, 2021
- 2 min read
The upstream industry is no stranger to barren times of investment but in 2020 this was coupled in the face of a global pandemic where the pinch and uncertainty was seen Worldwide and industry wide. This considered, there has been a trend over the last number of years for operators to move away from traditional methods of connecting pipework due to safety concerns, high associated costs, and availability of skilled trades for traditional methods of pipework fabrication.
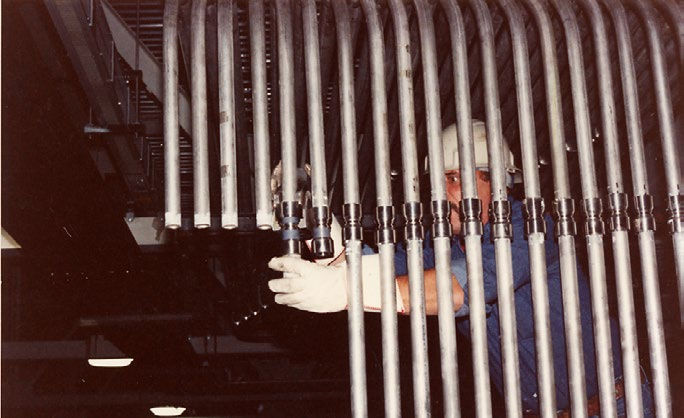
The mechanical connector has been around for an age, they come in all shapes and sizes with their various advantages but the age old trusted is the traditional weld neck flange. One of the key obstacles associated with flanged connections is their inclination to leak over time. This can lead to Technical Safety assessments and the case for area’s to be re-classified. The challenge then becomes how do operators keep a “cold work solution” whilst eliminating the baggage of potential leaks from flanges – Lokring Coupling to the rescue!!!
A Lokring coupling is the only mechanical joint on the market today that is equivalent to a coded butt-weld and is capable of being used in place of two flanges without the need to derate the classification of a zone from a “fully welded” system. The cost/time benefit of using a Lokring coupling over two flanged joints is generally well established within industry.
In 2016 an offshore operator in the North Sea requested assistance from a leading global energy consultancy group to carry out an assessment of Lokring with the view of using the weld equivalent technology on a fuel gas application offshore. This document was used to fully back up claims made by Lokring, and as justification to carry out the works. Direct quote from the document – “Lokring could be viewed as equivalent to welded pipework, for fuel gas, keeping the area classification as a non-hazardous zone.”
Please consult Lokring UK in their Aberdeen office if you would like to learn more.

Kommentare