Trelleborg’s Fibre Reinforced Thermoplastic Helps Increase Service Life of Offshore Rig Equipment
Material selection and design processes are becoming increasingly critical to the success of oilfield tool and production systems, as higher pressures and temperatures are being reached, and equipment lifespans are expected to be 10 to 20 years.

Where sensitive electrical and data transmission is vital to achieving goals, especially in newer intelligent systems, such as measurement while drilling (MWD), logging while drilling (LWD), and wireline systems, performance ratings often exceed the capabilities of established materials such as thermosets, alluminum, steel, and titanium.
Various well logging tools require composite structures, often because of the composites’ high electrical resistivity or low electromagnetic radiation interference. Engineering grade Fiber Reinforced Thermoplastics can be used in high pressure/high temperature (HP/HT) applications or other environments requiring materials with outstanding chemical resistance. Thermoplastics tend to have higher initial costs but can survive significantly longer than thermosets.
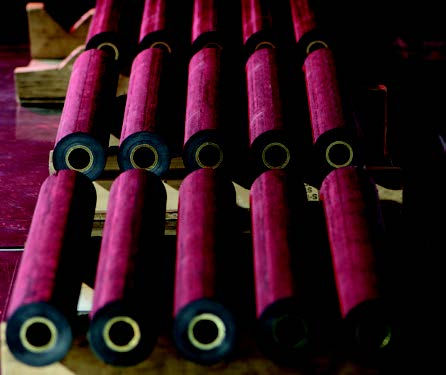
Fiber placement technology, such as that developed by Trelleborg Sealing Solutions, allows thermoplastic composite structures to be built up strip-by-strip, layer-by-layer, until the final shape is produced. An in- situ automated process melts and freezes resin on a strip of tape and bonds it to the previous layer.
This streamlined processing has many advantages over oven- or autoclave-cured thermoset processes. Benefits to part performance, include extreme repeatability, avoidance of the fiber buckling suffered with de-bulking thermosets during their cure cycle, and the prevention of high thermal induced residual stresses from a long-soak cure cycle.
More demanding downhole applications often require continuous fiber composites, predominantly because of their higher modulus and strength when compared to short fiber composites. These applications include antenna shields on various measurement technologies on LWD tools, electrical/structural isolators (gap subs) on M/LWD (measurement/logging while drilling) and wireline resistivity tools, and housings and logging sleeves for wireline resistivity tools.

Trelleborg Sealing Solutions has delivered parts for several applications using continuous fiber composite technology. One oilfield application where this has proven to be especially useful is structural insulators in titanium stress joints for offshore deep-water platforms. Here, sea water motion produces high bending movements on the riser and consequentially at the vessel attachment point. Using composite isolation cones protects the joint from wear and galling, and acts as an electrical insulator preventing galvanic corrosion of dissimilar metals used in the joint assembly.
The increasing awareness and demand for thermoplastic composites by specifiers is leading to an increase in efficient manufacturing and lower raw material costs year-on-year. As testing in harsh environments continues to show excellent performance results, confidence in fibre reinforced thermoplastics means they are becoming an alternative of choice to metal and thermoset materials for critical components in the oil and gas industry.
Comments