Articulated Arm Designed and Built for Amarinth Ltd
- Robert Robinson
- Sep 16, 2021
- 4 min read
Rotaflow is a global leader in swivel joint design and manufacture. We engage with clients all over the globe to produce swivel joints for a wide range of industrial uses, from food and drink production, pharmaceutical, process & plant to subsea oil and gas extraction. If there’s a need for a swivel joint in an industry, there’s a better than not chance we’ve supplied it!
A large part of our business is in the custom building of swivel joints. When clients have specialist needs, or an off-the-shelf solution simply won’t do, our in-house team of designers and engineers will produce swivel joints fit for specific purpose. Thanks to the tried and trusted reputation Rotaflow has built up over 4 decades, clients return to us again and again for their swivel joints.

One such custom design was for Amarinth Ltd, the global pump manufacturer. They had approached us with a problem that was going to require a custom solution, because off-the-shelf simply wouldn’t work.
They asked us to design and build an articulating arm that will serve as a part of their pump testing equipment. The arm is designed to enable efficient connection to variously sized pumps. Our design ensures that the pump testing process is smooth and effective, saving a lot of wasted time for Amarinth and their customers.
In a world where time and efficiency are of utmost importance, any delays can be costly. By engaging Rotaflow to design the articulating arm, it reduces the time taken to test the pumps. In manufacturing every small saving of time adds up, shortening the overall process and reducing the time is takes to deliver products to customers.
Technical Aspects of the Articulating Arm The arm has 4 10" Swivels to provide the range of articulation required. It has to cope with a lot of positional manipulation, so having 4 points of rotation make this possible. We design as efficiently as possible and this was the minimum we could fit into the arm and still enable it to deliver all of the movements and functionality required.
The arm is designed for operation 50 Bar. At Rotaflow we have the capability to pressure test every joint we produce even in our custom-built hyperbaric testing chamber if the application requires. We have tested the arm at Rotaflow to 75 Bar, so can be satisfied it is more than able to cope with the tasks set for it.
By testing in‑house we can adapt designs based on data and can be confident that everything we send out of the door is absolutely fit for purpose and certified as so. It also reduces our lead times on equipment – all of our designing, manufacturing and testing is done in-house, so we don’t have to factor in long delays as products are sent off site for testing.
This element of control also allows us to accurately forecast a completion date for a project, so both our team and our customers know what to expect and when to expect it.
The dynamic sealing surfaces have been overlaid with Stainless Steel to provide corrosion protection to the most important sealing surfaces. We have our own multi-stage method of overlaying stainless steel that has been developed over many years. It’s a process that means we can be very confident about the level of corrosion resistance the sealing surfaces have.

This design allows for the use of lower cost Carbon Steel for the rest of the structure without compromising build quality. This approach provides strength and structural integrity where it is needed most, but the appropriate use integrity where it is needed most, but the appropriate use of lower-cost materials saves the customer significant amounts of money.
Lifting lugs were provided at positions as required by the customer. The custom design process means that we can adapt our products to suit the exact requirements of the client. We produce equipment for a huge range of spaces and conditions, so our designers have a lot of experience in this area.
The final connection flange is a 'Lap Joint Flange' which allows the final connection to the pump to be orientated as required. This is a particularly important detail because it’s the final connection between the arm and the pump. It has to be sufficiently secure, easy to connect and disconnect and able to move wherever the testing dictates. The arm is PED cat I certified.
In order for the unit to be despatched in the most customer friendly fashion we organised specific same day despatching as this removed any issues faced with dealing with the somewhat awkward size and shape of this bespoke unit.
Rotaflow Quality Speaks for Itself
As a global supplier of swivel joints, Rotaflow have built a reputation for excellence. Our in-house team manage the job from end to end, so we do the design, manufacturing, testing and shipping. This streamlined operation removes all unnecessary costs and time delays from the process, making working with Rotaflow a faster and often less costly experience.
With 4 decades of experience and a global reputation for excellence, working with Rotaflow will guarantee your project is in the safest possible hands. From consultation to shipping, we’re experts in project delivery. Having designed and manufactured thousands of swivel joints for a huge range of purposes over the years, there’s little we haven’t seen before.
We build deep, long term relationships with our customers that see them returning time and again for different products on their other products. We also offer a refurb and replacement service, whereby we’ll refurbish Rotaflow parts if it’s appropriate to do so. It’s a testament to the quality of our products that some clients have had our swivel joints in place for literally decades!
Working with Rotaflow
We’re based in the Peak District and our central location means we’re easily accessible for all corners of the UK. If you have an engineering problem and would like to speak to the team at Rotaflow, you can reach us via the following options.
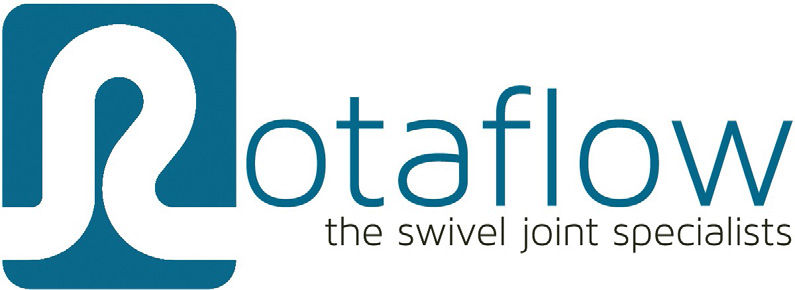
Comments