DEVELOPMENT OF MANUAL HOISTING EQUIPMENT
William Hackett has developed a second generation range of manual hoists to deliver performance ratios and functional enhancements which include new safety features and enhanced corrosion protection. These developments will provide operational benefits and extend the economic life expectancy of the equipment.
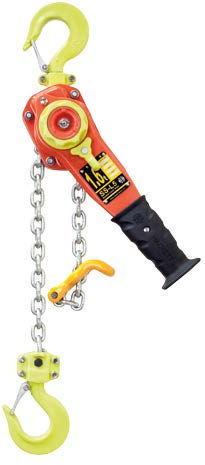
William Hackett is committed to continuous improvement of its products. Recent development work has focussed on its specialist range of manual lever hoists and chain blocks for use in the offshore sector, including the SS-L5 subsea lever hoist, ROV SSC4 subsea chain blocks and SS-C4 chain block for surface applications.
These products have been developed for use in harsh environmental conditions, and to meet and exceed the requirements of international standards. This includes:
• British Standard BS EN13157:2004 + AI:2009
• American Standards: ASME B30.16-2012 – Chain Block and ASME B30.21-2014 – Lever Hoist Australian Standard AS1418.2-1997
• South African Standards SANS 1594:2007 – Chain Block and SANS 1636-2:2007 – Lever Hoist
• NORSOK R-002: 2017
In addition, products have been subjected to salt water immersion and hyperbaric tests independently verified by DNV-GL and Tyne Subsea. The DNV-GL ‘Saltwater Immersion test verification, Report No. A0359376.02, Rev.1 verifies that the SS-L5 type subsea lever hoist could be safely used over a 21-day single immersion and a 31-day multi-immersion period.
The design features, testing criteria, and guidance for use, maintenance and storage of the SS-L5 have also been developed in line with:
• BP document DEV-AAD-SSSD- BP-0545 ‘Specification and compliance requirements for lever hoists used subsea on BP projects’
• IMCA DO28 June 2017 Rev.2 ‘Guidance on the use of chain lever hoists in the offshore subsea environment’
• IMCA Document SEL-019:2007 ‘Guidance for Lifting Operations’
The William Hackett hoists can be used within an operating temperature range of -40˚C to +55˚C, provide over 500hrs of protection against salt spray tests in accordance with ASTM B117 and ISO 9227, and include the following generic design features and specification:
• Light load capability of a better than the industry standard of 2% of the rated capacity.
• Construction and design minimises ingress of contaminants to the internal mechanism and brake surfaces.
• Twin offset pawls as standard – captivated internally as a secondary safety function by stainless steel springs.
• Stainless steel fixings.
• Sintered/fused friction material is used in the brake mechanism incorporating grooves enabling water to be dispelled from the friction surface more effectively during subsea operations.
• Load chain in accordance with BS EN818- 7 Grade 8 to mitigate the risks of hydrogen embrittlement.
• Corrosion protection of the complete brake mechanism including the pinion shaft , disc hub, change gear, ratchet gear, pawls, pawl stands and load sheave. In addition the load chain guide, stay bolt and chain stripper are also corrosion protected.
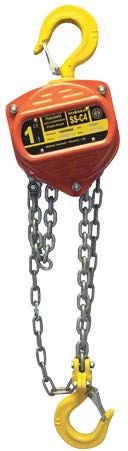
All of the manual hoists’ painted components including the casing, side plates and load hooks go through a dual coating process. The first process for the components consists of a phosphate bonding. Since use of Cr6 (Chromium 6) is restricted, it has been superseded by phosphate coatings giving enhanced corrosion resistance and surface adhesion. The second process consists of an electrophoretic paint outer coating that is dried and cured after application creating a high chip resistant finish.
In addition, the SS-L5 subsea lever hoist includes a dual anti-lock brake system that provides a two stage neutral process to engage rigging mode. The dual anti lock brake increases diver efficiency and safety by removing the need for the operative to return to the hoist grip ring to reset the hoist. The dual anti lock brake function acts like a car seat belt that engages when it senses inertia and it then releases under control as the tension is removed. In addition the adjustable travelling end stop allows the diver to engage a secondary manual safety system that is designed to match the Working Load Limit (WLL) of the hoist and provides the diver with a visual indication as to the status of the hoists brake mechanism.
All products are designed to achieve a minimum breaking load of 4 x the WLL; the load chain anchors / end stops are tested to at least 2.5 x the WLL with no restriction of either the brake or gears; and all products are individually proof tested to 1.5 x the WLL. Current development initiatives include an enhanced safety feature for lever hoists and chain blocks which will be introduced during 2018.
All of William Hackett’s business activities are controlled within a quality management system accredited to ISO 9001:2015 standard. The company has developed market leading product traceability and certification systems to ensure complete fulfilment of all customer quality requirements. William Hackett is also proud to be a member of the Lifting Equipment Engineers Association.
For further information about William Hackett, its products and services, please visit: